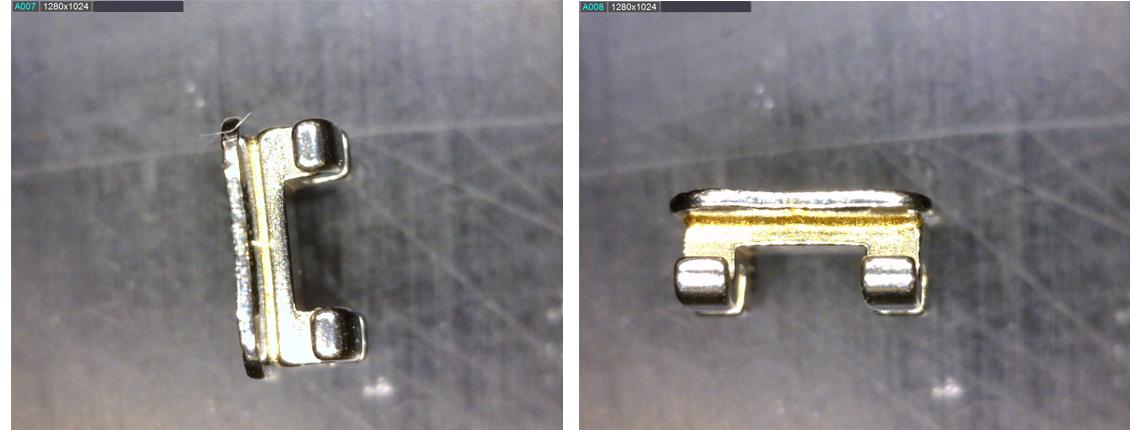
Post Braze Discoloration
Sep 13, 2022
The Problem:
A Prince & Izant customer was experiencing issues with discoloration on post-brazed bracket and plate assemblies.
Prior to the visit, P&I engineering determined what critical factors they needed to consider to assess the customer’s specific brazing process:
- Material and assembly analysis
- Braze process
The Process:
P&I Engineering scheduled an onsite visit with the customer for a full walkthrough and overview of the process as well as a detailed discussion of the findings.
- The current brazing cycle utilized a temperature of 1980°F at a speed of 9 in/min. This can be compared to a liquidus of 1475°F for the alloy that’s being used.
- Trials had been conducted per the previous supplier recommendations which was to braze samples at temperatures ranging from 1730-1780°F in hopes of minimizing the spread of the silver alloy. These trials included two different belt speeds, 9 in/min and 12 in/min, as well as varying amounts of alloy ranging from 1-3 dots. The trials were also conducted with 2 different assemblies, one with similar radial curvatures (decreased joint clearance) and one with mismatched curvatures.
- Examination of the assembly and brazing process did not reveal any major concerns. It was explained that the ultrasonic cleaning agent contains a chemical which may introduce sulfur to the assembly surface. However, it was determined that the primary focus should be to limit the spread of silver across the assembly rather than minimizing sulfur exposure, due to the fact that additional exposure may be experienced downstream which can generate the same discoloration.
-
A series of trials were conducted with varying temperatures, belt speeds and amount of braze alloy in an effort to determine ideal parameters for minimizing heat exposure while still ensuring successful brazing and optimal efficiency of the process.
The Findings:
- SEM examination displayed silver across the majority of the base component surfaces, due most likely to flashing (excessive wetting of the alloy). Discolored regions were determined to be a result of silver sulfide crystalline growth on the surface of the base components and braze joint.
- Results on the various trials were mixed, but it was determined that the majority of assemblies which passed tensile and shear testing were those which had a smaller joint clearance (better fit). This is consistent with the concept that appropriate joint clearance promotes increased capillary action, leading to a stronger bond. The dissimilar assemblies, which most frequently passed mechanical testing, utilized the highest volume of filler metal (3 dots), suggesting that more filler metal was required to fill the larger amount of free volume within the joint.
- Discoloration may be inherent to the material. Silver is susceptible to tarnish and corrosion by sulfur as well as chloride. If discoloration is deemed unacceptable within the braze joint, then it would be worthwhile to discuss alternative alloys. Depending on application, an introduction of palladium to the silver copper system has helped minimize corrosion susceptibility.
The Outcome:
Based on the information, it’s reasonable to assume that bulk discoloration of the part is a result of undesirable wetting (flashing) of silver across the surface of the base components. Generally, flashing is caused by several factors:
- Exposure to excessive heat, either through high temperatures or prolonged soak time
- A larger than recommended joint clearance where capillary forces are minimal, allowing the alloy to “fall out of” the joint and run across the surface of the parts.
- Alloy placement and assembly configuration within the surface can affect the direction of flow. Excess alloy applied to the joint can also lead to flashing.
Are you experiencing a related issue? If so, contact us to discuss alternatives specific to your needs.