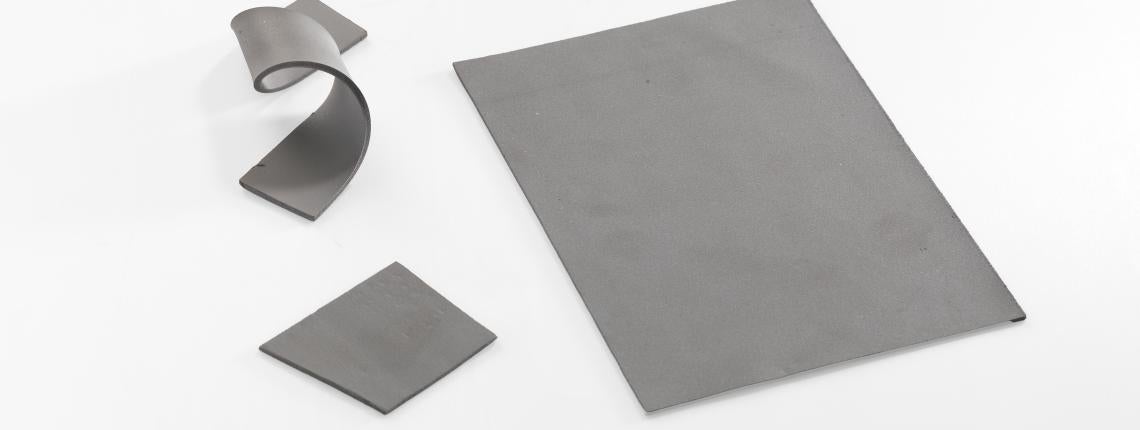
Manufacturing Pre-Sintered Preforms
Aug 07, 2023
What is a Pre-Sintered Preform:
Pre-Sintered Preforms (PSPs) are the product of sintered powders. The powders are custom blends of a superalloy and braze powder(s) heated to sintering temperatures to form plates. The sintered plates can be cut into specific shapes (preforms). Although PSPs are used in a variety of manufacturing process such as medical, mining, ceramics and powder metallurgy, the most common use of pre-sintered preforms is on gas turbine engines. The heat, stress, oxidation and extreme conditions inside an engine cause wear & cracking on the surface of many components. PSPs provide a reliable, repeatable, and lower-cost repair method to salvage parts. Repairing these parts is a large cost savings in contrast to completely replacing the damaged turbine parts.
Step-by-Step Overview:
- Blending Powders
- Mixing powders into Blended Paste
- Producing Blended Tape from paste
- Sintering the tapes into Plates
- Cutting Pre-Sintered Preforms from the plates
Manufacturing Process:
Blending Powders
The initial step of creating a PSP is creating a blended powder. This blend will consist of one (or more) superalloy powder(s) and one (or more) braze powder(s). Depending on the desired qualities of the finished pre-sintered preform. Customers can specify their desired alloys or request a recommendation from P&I's experienced metallurgist.
Prior to any blending taking place, these powders are produced by gas-atomization which results in a spherical shape or morphology. The particles for each alloy are classified by size using a process called sieving. The final final combination of sizes used is called the Particle Size Distribution (PSD). Most powders used in the PSP process are between 100 - 10 microns. Prince & Izant can utilize any desired particle size distribution, but prefers to use a proprietary blend of sizes to achieve the highest quality tape and sintered products.
Many customers specify the blend of powders used in their products depending on the end use of said products, while others take advantage of the engineering expertise at Prince & Izant to make recommendations based on the conditions and desired performance of the final product.
Now that individual powders are selected, it is time to create a homogenous blended powder. The amount of each powder is controlled by the weight percent of the overall blend. What does that really mean though? Let's look at an example of blending 100 lbs at an 80/20 blend-ratio; 80% superalloy, 20% braze powder. The operator will add 80 lbs. of the superalloy-powder and 20 lbs. of braze powder. Traditionally, the ratio of the superalloy is higher than or equal to the braze powder.
The mixture of powders is then put into a V-blender. A V-blender is two hollow cylinders (Imagine paint cans) attached together at an angle of 75 to 90 degrees hence looking like the letter “V”. The blender performs a full 360 degree rotation anywhere from five to 25 times per minute. The powders fall randomly within the vessel of the V-blender causing the powders to become homogenously dispersed.
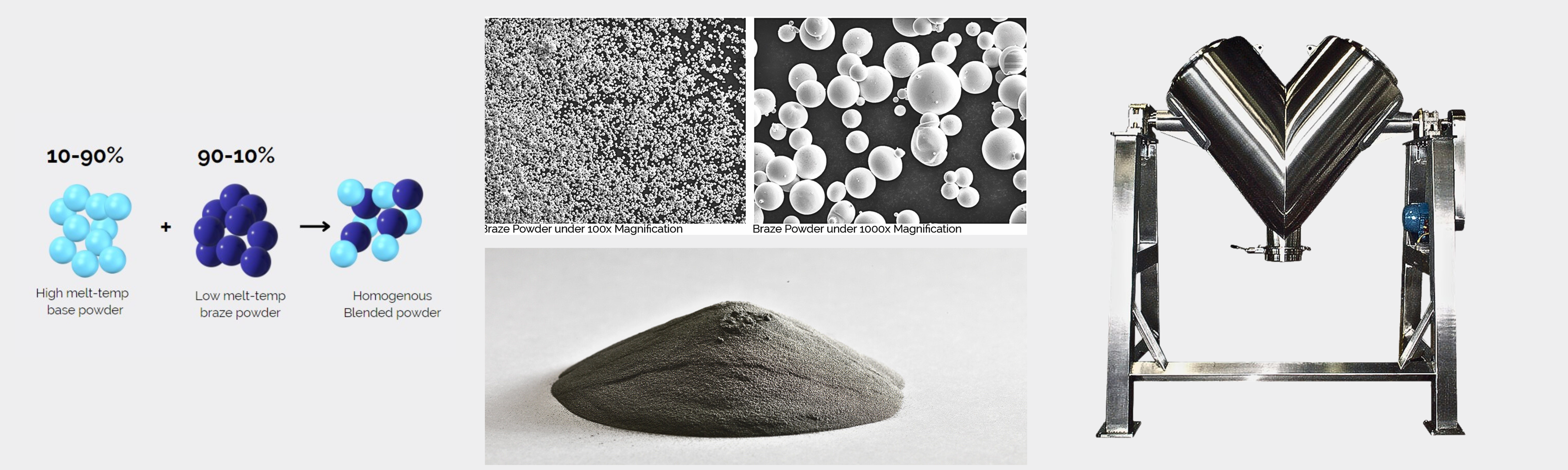
Blending Powders
The blended powder is then mixed with a suitable binder to form a bended paste (or slurry). Prince & Izant has developed custom binders which allow the powders to be formed into specified geometries. In certain situations, a thicker blended paste is preferred, other times, a less viscous blend like a slurry is ideal. The different binders created by Prince & Izant include varying amounts of solvents, polymers and other additives to ensure that the powders hold the desired shape without settling. The blended powder and the binder are mechanically mixed using different styles of mixing equipment including paddle mixers, roll-mixing and centrifuge mixers.
This viscosity (thickness) of the paste depends on the thickness of the tape being produced. The goals is for the binders to produce a flexible tape with the blended powder being homogenously suspended. The binder ingredients must be able to reduce cleanly during the sintering cycle without leaving any porosity, carbon or residue.
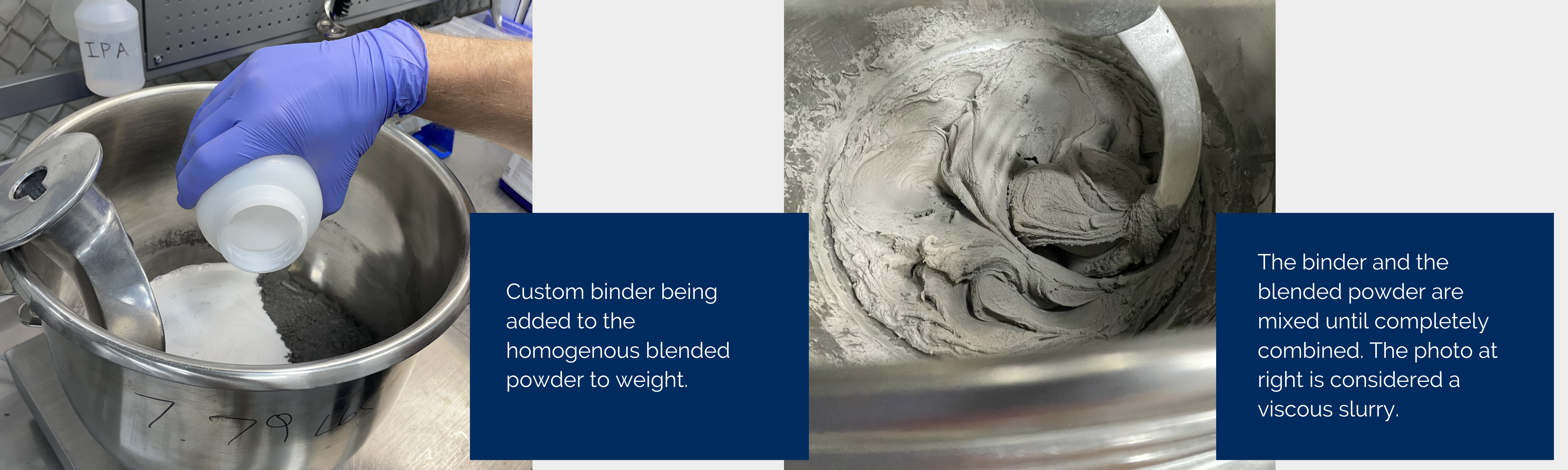
Blended Tape
The blended paste is formed into a rectangular shape of desired thickness, width and length called tape. Tapes can be produced in a wide range of sizes with common thicknesses ranging from 0.005" - 0.250". The length can be set or continuous on a roll. Once the paste is put into tape form, most of the solvents from the binder are no longer present, which leaves powder particles held together with the polymers and other additives from the binder system.
There are a few critical features of tape production. For one, the correct viscosity is needed to allow shaping of the paste while keeping the blended powders suspended in a uniform blend with no settling (the heavier particles sinking to the bottom). Controlling the thickness of the tape with tight tolerances is crucial as well. The thickness is of the tape is driven by the shrinkage that will occur during the sintering cycle.
By knowing the exact reduction in thickness that will occur during sintering, our engineers choose a target thickness for the tape. If the tape is produced with settling then it will undergo non-uniform shrinkage or distortion during the sintering cycle—meaning the tape may be thicker in some areas, “wrinkly”, or not have uniform mechanical properties.
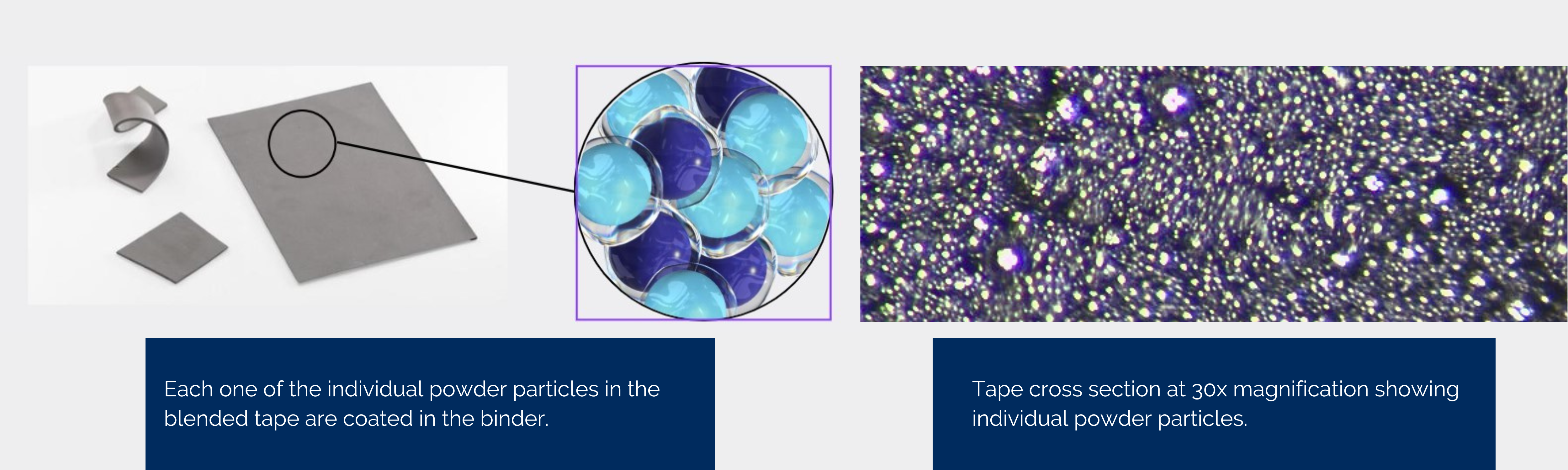
Sintered Plate
Blended tapes can be cut into specific length & width dimensions (taking into considering sintering shrinkage), then loaded on to racks and sintered at high temperatures in a vacuum furnace. The temperature to which the tapes are heated to in the furnace directly relates to which powders were included. Every powder has a different melting temperature. The Prince & Izant sintering cycles are proprietary and designed to achieve a high-density sintered plate. The plates are sintered flat, but are strong enough to be bent or contoured to curved surfaces.
While in the furnace, the tapes are heated to a temperature above the braze powder solidus temperature, but below the melting temperature of the superalloy. The braze powder either partially or fully melts forming a dense plate with the un-melted superalloy powder suspended uniformly throughout the PSP.
As the vacuum furnace heats up during the sintering cycle, the remaining binder (polymers and additives) in the tape are completely reduced causing the tape to condense or shrink. The plates shrink further yet during the liquid-phase sintering. Prince & Izant PSP plates have densities ranging from 95%-99% dense depending on customer specifications. After the plates are sintered, their thickness is measured using micrometers.
A small section of the plate is cut, mounted & polished. The image is evaluated for density by a software program.
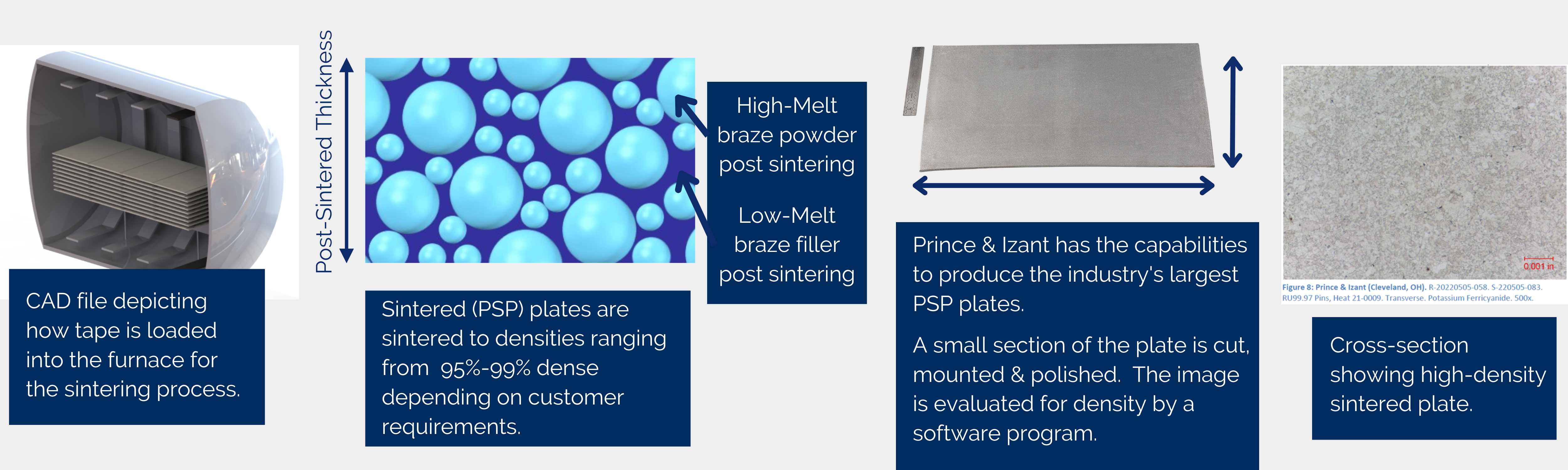
Cut Pre-Sintered Preforms:
P&I can supply PSP plates to customers who prefer to cut their own preforms or we can cut preforms to exact geometries listed on prints or from CAD files. P&I can also design custom geometries for customers using the base components being repaired. These preforms can be packaged in kits based on desired quantities.
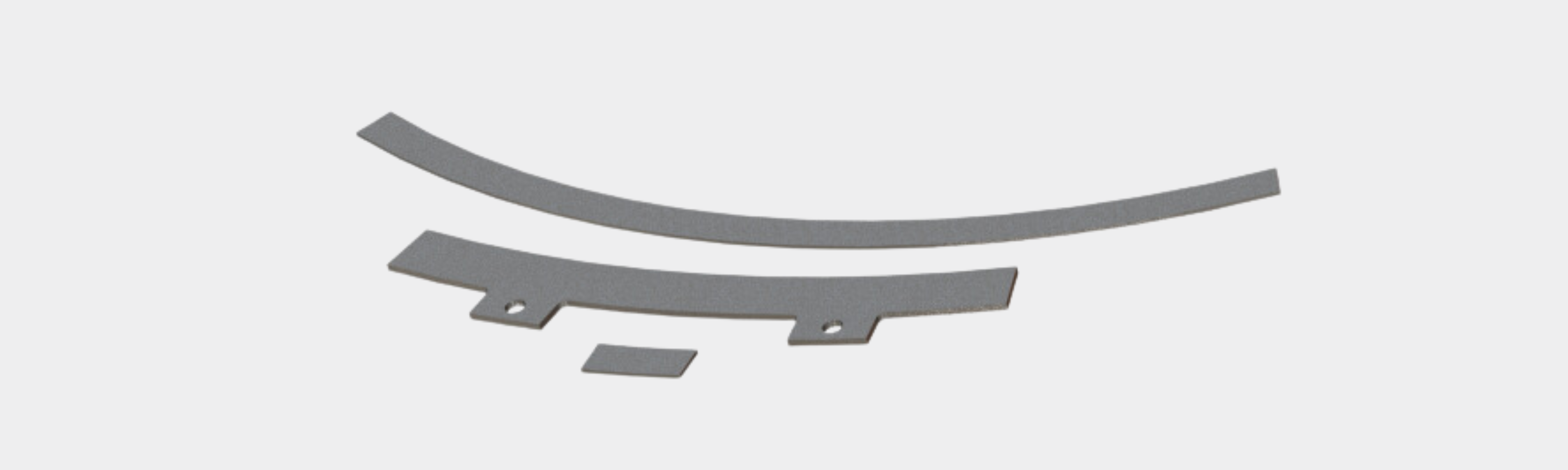
Applications:
Pre-sintered preforms are found valuable in numerous different industries due to their versatility, customizable properties, and the unique manufacturing advantages they provide. A few particular industries in which pre-sintered preforms are commonly used are aerospace, automotive, medical, electronics, and energy.
Crack Repair
In the aerospace sector, pre-sintered preforms are frequently employed to produce essential parts. Turbine blades, fuel nozzles, heat shields, and other aerospace components can be made using them because they can be formed into intricate designs. Pre-sintered preforms are well suited for addressing the demanding criteria of aerospace applications, including weight reduction, high strength, and temperature resistance, due to their excellent dimensional accuracy and material efficiency.
Surface & Dimensional Restoration
Pre-sintered preforms are utilized in a variety of applications in the automotive sector. They are used to produce parts for turbochargers as well as pistons, cylinder liners, and valves for engines. The dimensional accuracy and improved mechanical properties of pre-sintered preforms contribute to enhanced engine performance, fuel efficiency, and durability.
Tip Repair
Pre-sintered preforms are widely used in the medical industry. They are utilized to make surgical equipment, prosthetics, dental implants, and orthopedic implants. Pre-sintered preforms can be made in any shape and material composition to provide patient-specific implants with tailored features that improve biocompatibility, functionality, and patient outcomes.
Plugging Casting Holes
The electronics industry relies on pre-sintered preforms for various applications. They are employed in the production of electrical contacts, substrates, heat sinks, and other elements of electronic packaging. Pre-sintered preforms are well suited for heat dissipation and stable electrical connections in electronic devices due to their high thermal conductivity and dimensional correctness.
Improving Oxidation Resistance
The energy industry capitalizes heavily on pre-sintered preforms. They are employed to manufacture heat exchangers, boiler parts, and turbine blades, among other energy-related components. Pre-sintered preforms are ideal for high-temperature settings found in power plants and other energy systems because of their exceptional temperature resistance and mechanical strength.
P&I PSPs:
P&I can offer proprietary braze filler metals especially suited for superior creep strength, corrosion resistance, and oxidation resistance. Please contact us for further information